Pan granulation fertilizer production line project solutions
Basic inquiry information on the fertilizer granulation line
Enquiry for the Quartz Sand dust &fines Palletizer/ Granulator.
Dear sir, we are a leading glass bottle making company India with any our own Quartz sand manufacturing facility. During the manufacturing, we are generating a lot of sand dust & fines (100 to 400 mesh) which we are not able to use. Now, we are planning to use the Sand dust & fines in manufacturing of the glass bottles by using it instead of the manufactured sand in the glass furnace. Since the sand dust & fines cannot be fed into the furnace directly as it is very fine, we need to form small pallets instead of the manufactured sand in the glass furnace. Since the sand dust & fines cannot be fed into the furnace directly as it is very fine, we need to form small pallets in a Palletizer before feeding in the furnace. Since the adhesive property of the sand dust & fines is very poor, we are adding some binders before palletizing/granulating (balls of dim= 2 to 5 mm) the same in a temporary arrangement. I understand that you are manufacturing Pallisters/granulator for the sand dust & fine. We would therefore like to get your technical & commercial offer for a 5 ton /hr. Palletizer/granulator system.
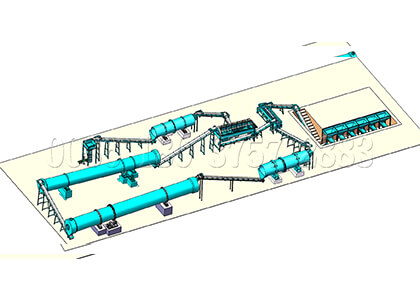
Brief introduction to the organic granule’s fertilizer production line inquiry from customer in India
Indian customer wants to produce granules materials with 5 ton per hour. The customer has a glass bottle making company in India. In his factory, there are lots of sand dust and fines wastes, so he wants to turn them into granules with additives like soda ash, sodium nitrite solution, and limestones. With a 5 ton per hour production capacity, the customer wants to make granules with an acre of 1360 square meters(40l*34mh) working space. This Indian customer has his own granulation line. However, in customers fertilizer production line, the rotary drum fertilizer granulator does not work well in his granule line, and its granulation rate is far lower than customer’s requirements. So, Indian customer want to find a new fertilizer production line solution from us.

5t per hour pan granulation production line solution to Indian customer’s factory
Based on Indian customer’s raw materials and production capacity, the company’s engineer team design a 5t/h production line equipped with pan granulator. In the disc pan granulation line, the main machine configurations are as follows:
The first part is raw material pretreatment machine
- 2030 forklift feeding machine: for customer’s powder material feeding.
- B600 8m belt conveyor for raw materials conveying.
- 20000mm diameter disc feeding machine for raw materials feeding.
The second part is machines used in sand dust granulating process
- 3000diameters pan granulator for sand dust and fines powder pelleting.
- B600 6m belt conveyor for granulated materials conveying
The third part is the rotary drum drier for granulated materials drying process
- 1.5*15 diameter drier for sand powder granules drying
- B600 6m belt conveyor for dried sand dust granules conveying
The fourth part is the dried granulated materials cooling process
- 1.2*12m diameter cooler for dried granulated sand dust cooling
The sixth part is the cooling granulated sand dust screening
- 1.8*7m diameter screen machine for unqualified granulated sand dust screening.
The seventh part is unqualified granulated materials crushing machine
- 600m diameter chain crusher for unqualified granulated sand dust grinding
- B500 10m belt conveyor for crushed granulated sand dust conveying
The eighth part is dust collecting machines for sand dust collecting
- Hot stove for energy supplying to the dust collection system
- 1200 cyclone dust collector for sand dust collecting
- 8c air induced fan for air supplying to the dust collecting system.
- 1200 cyclone dust collector for dust removing
- 6 C air induced fan for air supplying to the dust removal system.
- Dust collecting for dust collecting to the sand dusts.
How to solve customers’ problems on our pan granulating machine’s working performance?
In the sand dust granulation process, we recommend our disc granulator to our Indian customer. However, this customer fear it cannot make well granulated sand dusts as his required. In views of this, we recommend our customer send his raw materials to our factory for working performance testing.
How much quantity will be required for conducing the trails at our factory?
- Quartz sand dust, Size=100mesh to 500mesh
- Soda Ash, solid powder, sodium carbonate, Na2O3, Size:30mesh to 60meshmm
- Limestone, solid powder, Calcium carbonate. CaCO3, size= 5 mesh to 150 mesh
- Sodium silicate, Liquid, Concentration=50%W/W
- Customer wants to undertake the trials in our factory and want us send him back at least 5kg of Quartz dust granules (diameter=1mm to 5mm)
Resolutions to customer’s raw materials trial inquiry
Since customer’s trial materials are a bit of more, thus it will be more economic we buy the trial materials for customer and customer just pay for the trail material. This will be more economic and cost efficient on the trial process.
38 questions customer asked for the organic fertilizer production line?
1) Q: In fertilizer machines installation: The complete fertilizer granulation line can be installed in a building with length = 30-meter, width = 22-meter, height = 6 meter?
A: as your said, all the belt conveyor has 20-degree slop angle, the whole line length should be 34m, the width and height are ok.
2) Q: In the production line capacities: The plant output is 5 tons of finished granules per hour.
A: yes, granules output is 5t/h
3) Q: on the production line wastes emissions: Production yield of the plant = 100 % (means there is no waste generation due to operation)
A:the cover will be on pan granulators, on belt conveyor and on screen machine, so no more dust will suspend in the air. and the material in the dust collecting system can be recycled again.
4) Q:on the granulation rate of our machine: Minimum % of good quality granule production (without recycle).
A: the1-4mm size granules can be 90%
5) Q: on the unqualified materials screening: Maximum % of less than 1mm granules which goes into recycle.
A: <1mm granules size no more than 3%
6) Q: on the unqualified materials crushing: Maximum % of more than 5 mm granules which goes into recycle (through chain crusher).
A: it is about 7% granules size> 5mm
7) Q: On pan granulation system configuration: Can the granulator be of closed pan type instead of the open pan type as we feel that the closed type design has a better control on the granule quality & also controls the dust generation.
A: the granulator part can be covered by iron sheet house (reference following pictures) The dust won’t generation. Closed pan type design cannot be realized (because if closed, the material cannot be feeding into two granulators).
8) Q: on the dust collect system: The dust collector system should be adequate to ensure the dust level (SPM = suspended particulate matter) inside the plant should be less than 50 mg/m3.
A: the cyclone and dust collecting room and dusting fall room and water curtain dust collector can almost remove the dust fully. and as your requirements, the belt conveyors (colorful steel cover) and disc granulator parts (iron sheet house), and screen machine (reference number 16 answer) will have covers to avoid dust suspend in the air. all these designs can meet your standard suspending dust less than 50mg/m3.
9) Q: on the provision: Provision should be shown for the addition of liquid solidum silicate in the mixer in the final drawing.
A: you can check it in the final drawing, we designed for you on the granulation line.
10) Q: on the pan granulation line’s electric system: Please provide the motors and variable frequency drives of Siemens.
A: Yes, will quote machines price with Symons motor (440V, 50HZ) later, you can find them in the quotation later.
11) Q: On the granulation line machines operation: We would like you to let us know the Operation philosophy of the complete plant.
A: I think maybe you want to know how to operate and maintained the whole line. When installation, our engineers will be there to instruct installation, commissioning machines, and training your workers how to operate them, how to easy regular maintenance. And we will send you a PDF machine manual and document one when with machine delivery.
12) Q: On the whole organic fertilizer production’s automatic system: What is the level of instrumentation & automation considered. Is a completely automated or semi-automated plant.
A: except raw materials loading & finished granules packing & shifting which will be done through mono rail system, only 1 person need to feeding agricultural waste pellet to furnace.) the line is completely automated.
13) Q: on the workers costs of the 5 ton per hour organic fertilizer production line? How many people are required to operate the plant (include all the operations)? Mention the maintenance operations separately.
A: 3-4 workers will be needed: 1 for batching machine material feeding; 1 for furnace, 1 or 2 for packing machine.
14) Q: on the screening machine’s maintenance: On How frequently the rotary screen meshes needs to be changed. Do you recommend that we buy the spare mesh from you or you provide us with the drags for us to procure local?
A: half a year need to change the screen mesh for your material. we will provide a set SUS304 stainless steel spare mesh for you, its price is about 600USD.
15) Q: on the Cyclone system: We wanted to know if the Cyclone system will be effective in maintaining the dust levels inside the plant.
A: yes, the cyclone collecting dust effect is better than bag system (once your referred). you can see the dust collecting system effect in the video on WhatsApp.
16) Q: on the dust collect system configurations to different machines: You have only indicated dust collector system to be connected to the outlet of the rotary drier ,but we feel that there are other points of dust generation (like Granulator ,Rotary screen, Conveyors) which also needs to be removed through dust collector system. Therefore, we would like you to evaluate the sizing of the dust collection system. We wanted an ambient space where the dust level should not be more than 50 mg/m3.
A: For the granulator, conveyor, please reference number 7&8 answer. we can design a cover for screen machine, like this one to avoid dust generation.
17) Q: on the belt conveyors functions and configurations: Please confirm if the all the conveyors will be fully covered & sealed to control the dust from getting into the surrounding atmosphere.
A: reference number 8 answer.
18) Q: on the whole granulation plants components configurations: In view of the dust generation in running such plants, we would prefer that you use all the sealed bearings wherever possible, preferable of SKF, FAG, NTN makes.
A: No need to use the sealed bearings. because all the machines (machines that dust will generation) will be have a cover to avoid dust generation. using SKF, FAG or NTN sealed bearing will largely increase your budget. Please consider our advice.
19) Q: on the fertilizer machines electric motors supplier: What are the makes of the motors, can it be Siemens IE-3 motors.
A: yes, motor can be designed as your requirements. but the machine price will float up relatively.
20) Q: on materials processing and allocating: Can you please explain how the quantities & proportion will be controlled using the system provided.
A: the belt conveyor motor of the batching machine is inviter motor, so the belt conveyor moving speed can be regulated on the control box. It means you can control every belt conveyor running speed to control three material quantities & proportion. you can check the dynamic batching machine working video in WhatsApp.
21) Q: on additional tailored configurations to organic materials granulation line: Please include the Liquid sodium silicate storage tank in your scope.
A: You can check it in the drawing
22) Q: on the labor costs reduction to the production line: Kindly include all the equipment in your scope which is required to run this plant automatically with minimum manpower (except raw materials loading & finished granules packing & shifting which will be done through mono rail system). Please note that we will go for semi automation only if the automation system becomes more expensive. Kindly indicate the operations which the manpower is required to undertake so that we are very clear about the operating requirements.
A: except raw materials loading & finished granules packing & shifting which will be done through mono rail system, only 1 person need to responsible for furnace. other parts of this line are fully automatically.
23) Q: on the batching system operations: As this is a batch granulation therefore how will you control & modulate the continuous flow. Can you explain the operation?
A: by batching machine (material feeding parts), you can reference number 20 answers.
24) Q: on the manufacturing materials of pan granulators: What is the material of the surfaces of the granulator & drier which comes in contact with the quartz dust. Is there a possibility of Iron addition in the granules due to the same?
A: Both granulator and dryer material are Q235B boiler steel, which has high strength and not easily deformed characteristics.
25) Q: Regarding the combustion system, we do not have a source of natural gas therefore we would request you to give the option for combustion system which uses agricultural waste, sugarcane waste, cow dung waste, pet coke etc. Based on your recommendations we will try to source the fuels locally. The natural gas, furnace oil, diesel will be very costly to operate we prefer agricultural waste pallets with calorific value of 4000 kcal/kg.
A: the agricultural waste pellet is good fuel for dryer. can be used on this system.
26) Q: on the combustion system refectory materials. Your offer for the combustion system should include the refractory. However, additionally you can also give the quote for the refractories separately so that we can also try to see if the same can be sourced locally.
A: the refractory material of the furnace is fireproof cement and fireproof bricks. you can find it in your country
27) Q: on the fuel consumption of the 5 ton per hour granule making line. We would also like to know the fuel consumption of the recommended system for this 5 ton/hr. line.
A: for your 4000Kcal/kg agricultural waste pellet fuel, about 350kg pellet will be need for one hour for this line granules drying.
28) Q: on the dust accumulated system. Please indicate how the dust accumulated from the dust collector system can be reused & necessary conveying system for the same.
A: for the cyclone dust recycling, you can use a bag on the cyclone discharge port to collecting dust. and for the dust fall room, your worker just needs to clean it regularly (1 time for a week)
29) Q: on the complete fertilizer production line machines technical specifications: Please send the specifications sheet for the different equipment selected for our line.
A: yes, will send you the quotation with detailed specifications.
30) Q: on the packing machine specifications: Please details the scope of the packing machine along with the operations. Is it automated, semi-automatic & whether the manpower is required etc.?
A: you can find the packing machine details in the quotation later. packing weight range 500-2000kg. Just need 1-2 workers.
31) Q: on the battery limits of the machine: Kindly define the battery limits of your scope & also mention our scope of work.
A: you need to provide:
i. cutting machine
ii. crane
iii. welding machine
iv. 7-8 worker for installation.
32) Q: on the quality warranty of the granulation line: Please mention the performance guarantees for this complete granulation line.
A: One-year guarantee (Exclusive wearing spare parts). If any parts are found defectively in quality within guarantee, we shall replace them for free. Client should responsible for their own operation mistakes and man-made problems. After guarantee, we can provide all the machine parts with Ext price.
33) Q: on the payment terms of the fertilizer granule line: Also, the payment terms should have 50% advance & 50% after commissioning.
A: No, the payment term is 50% T/T deposit, the balance should be paid before delivery. When installation, our engineers will be there to instruct installation, commissioning machines until machines can work normally, and training your workers how to operate this line, how to easy regular maintenance. You just need to pay the round air tickets and 100USD salary /day, and accommodation.
34) Q: on engineer onsite technical supports: Please note that we need your engineer’s presence for at least 30 days in our plant after the successful commissioning to teach our Operators in operation & fine tuning the quality parameters.
A: please reference number 33 answers.
35) Q: on qualifications: Your system should be CE certified.
A: Yes, CE certificate can be had, you need to pay extra costs: 910USD.
36) Q: on engineer technical support costs: Your offer should consider a consolidated Installation & Commissioning charges & not on per day basis.
A: 100USD salary per day including the instruct installation costs, machines commissioning charges, and worker training costs.
37) Q: on the fuel power and manpower consumption of the total granule fertilizer plants. We would like to know the total power, fuel and manpower requirement to run this line.
A: Total powder of this line, you can find it in the quotation. fuel, reference number 25 and 27 replies.
38) Q: on total costs on the granules production: We would also like to know the approx. cost of producing the granules if it cost Rs 500 per man /day, power at Rs 7/kwHr, Agricultural waste fuel at Rs 10/kg, Furnace oil at Rs 45/kg etc.
A: approx. cost for one day: 38668.8Rs= 500Rs*4 workers+ 154.8 Kw*Rs7/KwHr* 8Hr+350kg*Rs 10*kg *8Hr
The above information is just a complete granule production line with a 5-ton output per hour, detailed information needed on other project solutions, ne free to contact us at any time.