Static composting is to stack the raw material mixture on a ventilating layer made of small wooden blocks, broken straw or other materials with good gas permeability. The ventilation layer is provided with a ventilation pipe, and the ventilation pipe is connected with the fan to supply the gas to the pile to complete the composting process. The difference with the windrow composting is that no material is turned over during the composting process, and a special ventilation system and a fan are used to forcibly supply oxygen to the pile.
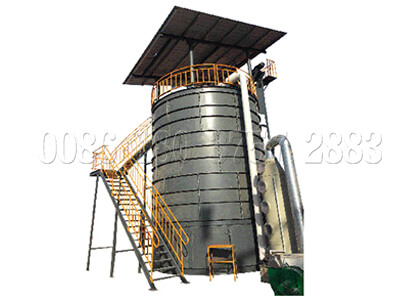
Static Composting System Origin
The static composting process was developed by the Agricultural Research Center of the US Department of Agriculture, BELTSVILLE, Maryland.
In 1973, the center successfully developed a strip composting process that uses wood chips as an expansion material to treat digested sludge. However, when the process was used to treat coarse sludge, it encountered the problem of producing odor. The ventilation static system was to solve Developed by the problem of fermentation producing odors, the process is called the “static composting” process, sometimes called the BELTSVILLE process. The state composting process has been widely used in the United States, with more than 76 facilities in operation in 1990.
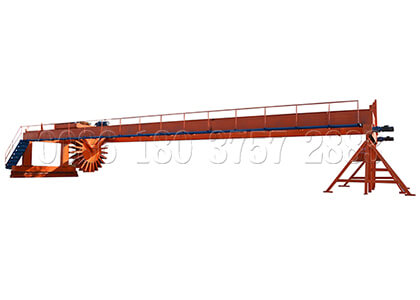
How to build a complete static composting system?
The compost of the matrix is usually added with an expansion material to adjust the porosity of the heap. Static compost uses pipes and blowers to supply gas to the stack. When the pipeline is built, there is no need to turn the raw materials. If the air supply is sufficient, the stock is evenly mixed and the composting cycle is about 3 to 5 weeks.
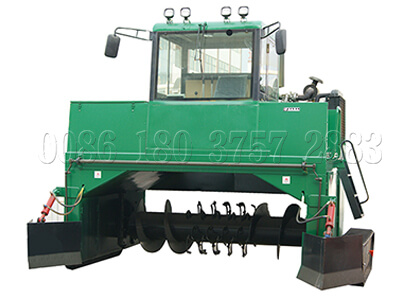
Static composting system construction
The static compost pile can be constructed according to the permeability of the raw materials, the weather conditions and the performance of the equipment used.
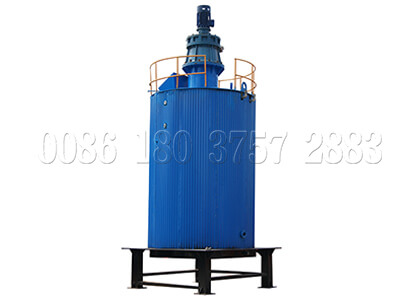
Pile height design requirements
Generally, creating a relatively high pile is good for preserving heat in winter. In addition, a layer of compost can be placed on the surface of the pile to moisturize, insulate, prevent heat loss, fly and filter ammonia and other substances that may be produced in the heap.
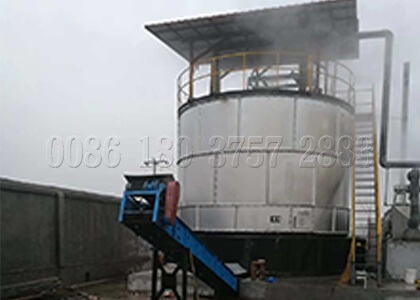
Composting pile length design
The length of the stack is limited by the conditions of gas transport in the stack. If the pile is too long, it is difficult to get oxygen from the farthest position of the blower, which may cause anaerobic, and some composting cannot reach maturity.
Add additives to the compost pile
It is often necessary to add a harder solid conditioning agent (such as straw and wood chips) to maintain a good aeration structure of the heap. In order to make the air distribution more reasonable, the manure or sludge must be thoroughly mixed with the conditioning agent before being piled up.
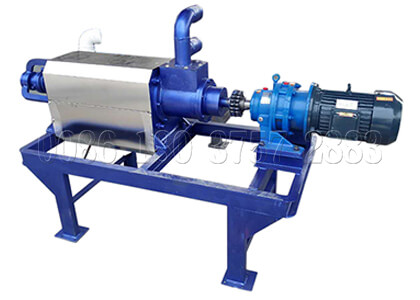
Ventilation control to the static composting pile
Ventilation is a key operation in the composting process because static composting does not turn over. Ventilation can be performed by forced ventilation or induced pumping to the heap.
Ventilation control methods
Timer ventilation control: Ventilation control usually has two methods, one is called time control method, and the principle is to use timer to control blast. It is a simple and inexpensive method, which can provide enough air to meet the composting pair by controlling the time. Oxygen is required, however, this method does not maintain optimal temperatures, sometimes temperatures can exceed the required limits, and the rate of compost fermentation is limited by the high temperatures.

Temperature control: The other is called the temperature control method. In order to maintain the optimal stack temperature, a temperature sensor (such as a thermocouple) is used for real-time monitoring. When the stack temperature reaches the set temperature, the electronic signal emitted from the sensor can be controlled, letting the blower work or stop. When the temperature reaches the set high temperature point, the blower starts to cool down; when the stack cools to the set low temperature point, the system turns off the blower. Compared to time control methods, the air blowers required for temperature control are larger and the airflow rate is faster, requiring a more expensive and advanced temperature control system.
-1.jpg)
What does the ventilation rate indicate in the static windrow composting process?
The ventilation rate is used to indicate the amount of air required per ton of dry solids per hour and is an important process parameter in the windrow composting process. According to the ventilation demand and the composition of the pile, the theoretical value of the oxygen required for most of the pile is l.2~2.0 O2/g volatile solids. Ventilation rates can be divided into minimum, average, and maximum rates. The maximum ventilation rate is usually 4 to 6 times of the average ventilation rate, and its influence on the intermittent composting process is greater than that of the continuous composting process. Epstein et al. believe that the spacing of the ventilation ducts is the key to the high temperature of the whole stack, and the ventilation should be 9 to 15 cubic meters / (h · t ds). The BELTSVILLE process usually requires 142 cubic meters/(h·t ds) of air volume to keep the reactor oxygen between 5% and 15%. The new design requires a ventilation of 56.8 cubic meters/(h•tds). At the peak, it is close to 142 cubic meters/(h.t ds) high air volume design is currently used without exception. In fact, the ventilation should be adjusted according to the specific conditions of each system.
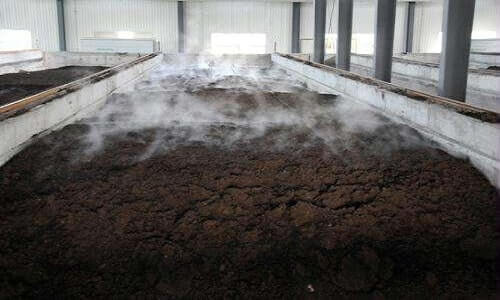
How to operate the static composting system?
The usual steps of the static composting system are as follows:
- Mixing the material with the conditioning agent proportionally;
- In the permanent snorkel or a temporary porous vent tube covering about 1 (cm) thick conditioning agent to form a compost bed;
- Add the mixture of material/conditioner to the compost bed;
- Overlay the surface of the pile with a layer of decomposed compost that has been smashed or unscreened;
- Connect the blast (air pressure) machine to the vent line.
The body begins to ferment, and the blower can blow air into the pile (forced) or suck the air out of the heap. In the inductive control mode, the exhaust gas from the blower can be collected, deodorized and discharged.
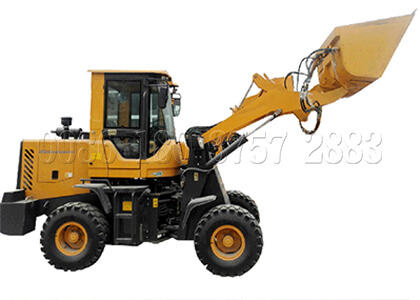
Expansion agent used in the static composting system
Considering that the expansion agent added during the wet matrix fermentation process is bulky and costly (such as wood chips), and the quality of the product can be improved after removing the large expansion agent, it is generally required to separate the expansion agent after the fermentation is completed and re-re- use. If wood chips or other degradable materials are used as the expansion material, there will be degradation and physical fracture during the fermentation process. Finally, some expansion agents will enter the fermentation material through the blinking due to the decrease of the matrix diameter, so that it needs to be added in the next fermentation. A new expansion agent to maintain balance.
Usually there will be some leachate under the heap. In the induced ventilation control mode, a pool must be set under the fan head to collect sediment. These leaching and sediment should be collected and treated.