Groove composting is actually a special type between windrow composting and stirred trough composting. The composting process takes place in a long and narrow channel called a “slot”. The track is erected above the channel wall. There is a turner on the track to turn over the material. The bottom of the tank is equipped with an aeration pipeline to ventilate and aerate the pile. It is a composting system that combines controlled ventilation with regular stacking.
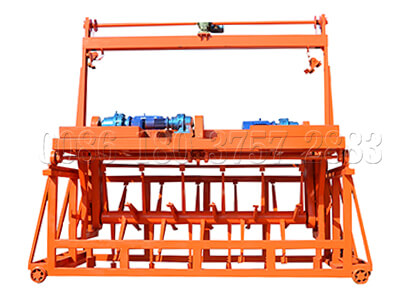
Groove composting technology history
According to available data, trough composting is a relatively new composting system that emerged in the middle of the 20th century. It was first proposed by the Japanese Okada Manufacturing Co., also known as the OKADA process. The METRO-WASTE process that emerged in the United States in 1966 consisted of a number of juxtaposed boxes (grooves), each about 6.10 m wide and 3. 0 m, length 60.96 ~ 121.92m, rails are installed on the wall of the cabinet, there is a cloth machine moving on it, and the pile is intermittently stirred by turning and moving forward. The PAYGRO process has also added an odor collection and purification system based on the above. In 1985, based on the Japanese trough system, 1N. The IPS process proposed by TERNATIONALPROCESSSYSTEMS is a typical tank composting system with a tank width of 2 m and a height of 1.83 m. The length of the tank is adjusted according to the fermentation time (generally 18 to day), and air is supplied from the bottom of the tank. The stacking material is input from one end of each tank, and is piled up once a day. Each time the animal material is moved forward along the tank by 3,05, 3.66m, the operation of the turning equipment is fully automatic, no operator is required. The system has 13 facilities in operation or construction in the United States in 1991.
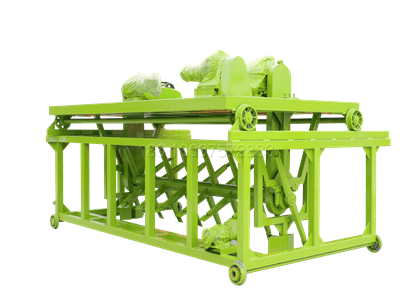
Groove composting system classifications
Considering the existing trough composting system, we can divide it into two types according to the way the material moves.
One is the whole-in and out-out type, which is to fill the whole fermentation tank once by the composting material through the cloth machine or the forklift, and through the different mixing equipment such as the hinged dragon and the barge, the compost material is ventilated, crushed, and maintained in porosity. The material does not shift during the whole fermentation process, or the displacement is very small. After the fermentation is finished, the material is removed by a discharge machine or a forklift.
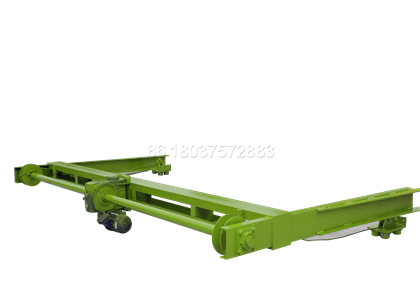
The other type is continuous. The turning of the compost material in the fermentation tank is completed by the agitation of the material, such as the chain plate and the hopper. Generally, the pile is once turned up, and the material can be in the fermentation tank. 2,4m forward, can also be transmitted through the belt for longer distance displacement. In the continuous composting fermentation, the raw material is placed on the first end of the tank by the cloth bucket. As the turner moves and stirs on the track, compost and mix the raw materials. Displacement to the other end of the trough, when the material is substantially decomposed, can just be removed from the trough. Because of its simple operation, labor saving and low energy consumption, this composting system has been widely used all over the world in recent years.
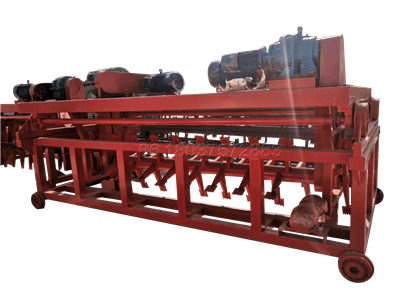
Compost tuning machines used in the groove compost turning system
The trough turner is similar to the windrow turner, which uses a rotating blade, screw, chain plate or roller to make compost. The material is turned to ventilate, comminute and maintain porosity. The current use of turners is highly automated and machine utilization. The control switch can work automatically, and some can also be remotely controlled. Most factory composting systems are equipped with aeration devices at the bottom of the fermentation tank for the purpose of rapid composting. Since the raw materials placed along the length of the trough are at different stages of the composting process, the blast chute is divided into different venting zones along the length direction. The trough composting system can use several blowers, each of which delivers air to the air. A zone of the tank and independently controlled by a temperature sensor or timer.
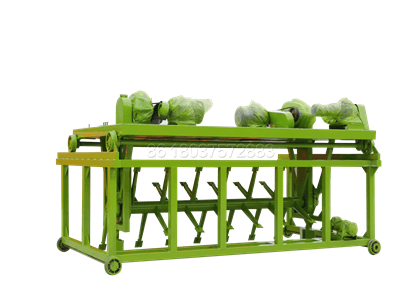
What is the capacity of the groove composting system?
The capacity of the system is determined by the number and volume of slots. The size of the trough must match the size of the stacker. For protection machine equipment and control of composting conditions, the tank should be built in a building or greenhouse. If you are in a temperate climate, you only need to add a roof.
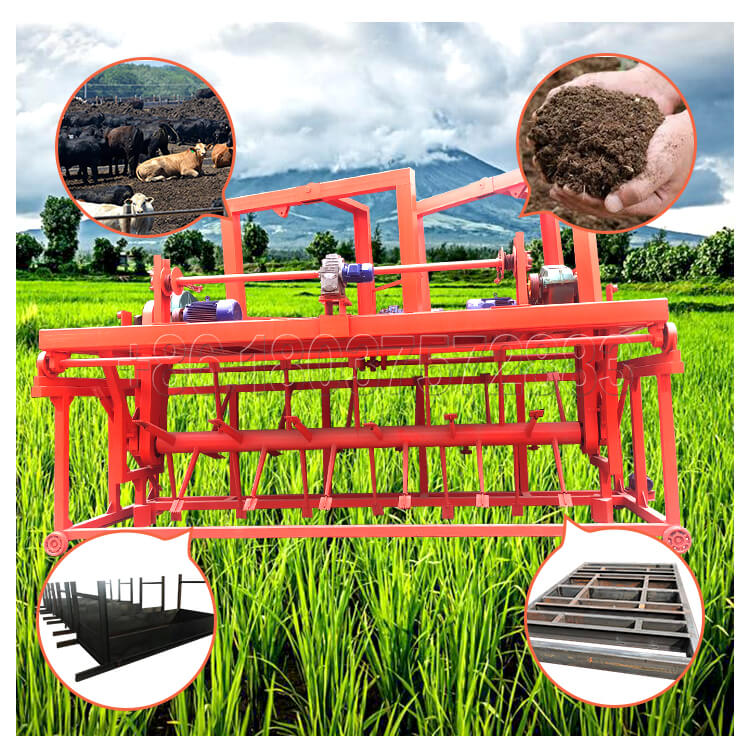
The length of the tank and the number of predetermined stacks determine the composting cycle. The recommended composting cycle of the blast tank composting system is 2~4 weeks. The biggest advantage of the trough composting system is that it has a small footprint, a short composting cycle, uniform quality of composting products and labor saving. At present, several units in China are conducting research and production of trough turning machines, and some large composting plants use troughs. Composting, the daily processing scale can be as high as 500 tons.