After the 1980s, countries around the world began to develop a large number of reactor composting systems, some of which were called “container systems.”
“The system” is also known as the “digester” or “fermenter.” The compost reactor equipment must have the function of improving and promoting the metabolism of microorganisms. During the fermentation process, it must be turned over, aerated, stirred, mixed, and assisted in ventilation. Such facilities or operations to control the temperature and water content of the heap, and also solve the problem of material movement and discharge in the reactor composting, and finally achieve the purpose of increasing the fermentation rate, shortening the fermentation cycle, and achieving mechanized production.
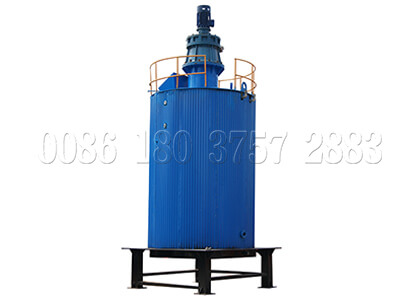
Reactor composting system classificaions
The reactor system develops rapidly, and different system types are out of layer. According to the flow direction of the material, the reactor composting system can be divided into: horizontal flow reactor and vertical DC reactor.
Horizontal flow reactor includes rotary chamber and agitation warehouse type; vertical DC reactor includes agitated fixed bed type and package type. The US Environmental Protection Agency divides the reactor composting system into: plug flow and dynamic hybrid. Population in push flow system Feeding, exporting and discharging, the residence time of the materials in the composting fermentation bins is the same in different time periods; in the dynamic hybrid system, the machinery is not used stirring and mixing the material.
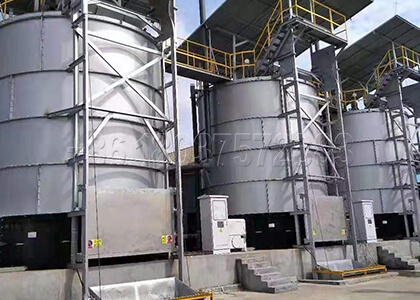
According to the shape of different fermentation tanks, the push-flow system can be divided into cylindrical reactor, rectangular reactor and grooved reactor; dynamic mixing can be divided into rectangular fermentation tower and ring fermentation tower is also divided into a passive ventilation reactor system, a forced ventilation non-stirred reactor system, a forced circulation stirred reactor system and a drum reactor system according to the ventilation mode, the presence or absence of agitation and the shape characteristics.
From the technical level, the technology and equipment of reactor composting systems in foreign countries have been gradually improved, and basically reached the level of scale and industrialization.
3 common reactor compost types
Silo type compost reactor
The reactor composting system is a silo that discharges compost from the bottom of the top feed. Each day, a rotating paddle or shaft is used to mix the compost material in the upper part of the silo, and the compost is taken out from the bottom. The ventilation system allows air to pass through the stack from the bottom of the silo, collecting and treating the exhaust at the upper portion of the silo. This composting method typically has a composting cycle of 10 days. The volume of the compost taken out per day or the volume of the refilled material is about 1/10 of the volume of the silo. The compost taken from the silo is often stacked in a second ventilator warehouse. Since the raw materials are stacked vertically in the silo, this system makes the footprint of the compost small.
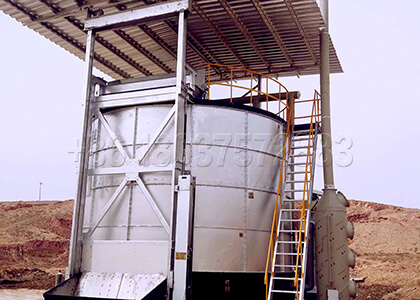
Despite this, the composting method still needs to overcome problems such as material compaction, temperature control and aeration, because the raw materials are not sufficiently mixed in the silo and must be mixed evenly before entering the silo.
Tower compost reactor
Fresh livestock manure, fermenting bacteria and various excipients required for fermentation are stirred evenly and then lifted into a multi-layer tower fermentation tank by belt or hopper equipment. The compost materials are continuously or intermittently input into these systems. The material is typically allowed to be periodically transported from the top to the bottom of the reactor, while being vented and dried in the tower by flipping the flaps. The characteristics of this composting system are provincial and provincial labor, but the relative investment is large and the equipment maintenance is difficult. The fermentation tower reactor designed by Chinese scholars Chen Haibin and Wan Yingfeng (2006) has a basic structure of sealed multi-layer fermentation tanks (3 to 5 layers). The bottom of each layer is a movable flap, and the fermentation raw materials are taken from the top of the device. After passing through the cloth device, the top fermentation chamber is sprinkled. After a certain interval, the fermented raw material falls under the action of gravity to the lower layer, and so on. The top of the fermentation tower is provided with an air outlet, and an external deodorization system is provided on both sides of the device. It is equipped with ventilation and exhaust lines, which will be introduced into the upper part of the movable plate through the gap of the movable flap, and discharged from the upper part or the top of the upper fermentation tank to realize oxygen supply and heat dissipation. The fermentation cycle is 4 or 6 days.
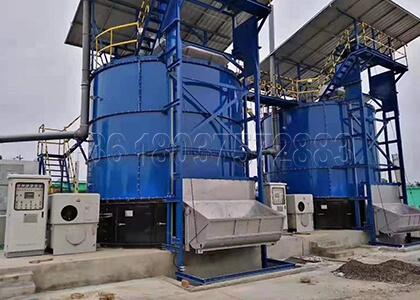
Drum type compost reactor
The drum compost reactor is a composting system that uses a horizontal drum to mix, vent, and output materials. The roller frame is on a large support and is flipped by a mechanical transmission. The composting process in the drum begins very quickly and the degradable material is quickly degraded by aerobic. However, compost must be further degraded, usually with strips or static aerobic composting to complete the second phase of the composting process. In some commercial composting systems, the stack remains in the drum for less than a day, and the drum essentially acts as a mixing device.
Ventilation is provided by the exit end of the drum, and the material is mixed with the air when it is turned in the drum. The direction of flow of the air is opposite to the direction of movement of the material. Near the discharge end of the drum, the compost is cooled by fresh air; in the middle of the drum, the temperature of the air stream rises and the rate of composting increases; at the population of the drum, a new pile is added, the temperature of the air stream is highest, and the composting process begins.
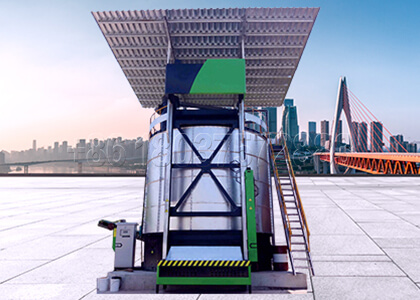
The drum can be a combined drum or a split drum. The combined roller moves all the stacks in the order in which they are loaded with the rollers. The speed at which the drum rotates and the inclination of the central axis of the drum during rotation determine the residence time of the compost. The management of a split drum is more convenient than a fitted drum. The split drum is divided into two or three bins, each bin including a moving bin with a moving door. After the end of composting every day, the moving door of the discharge end of the drum is opened, the compartment is emptied, the other compartments are subsequently opened and moved one after another, and a new batch of materials is loaded into the first compartment. Each moving door has a base to successfully achieve batch inoculation of microorganisms. The compost product can be directly transported from the discharge end to the sorting machine, the sorting machine removes large particulate matter, and the large particulate matter is sent back to the drum for further composting.